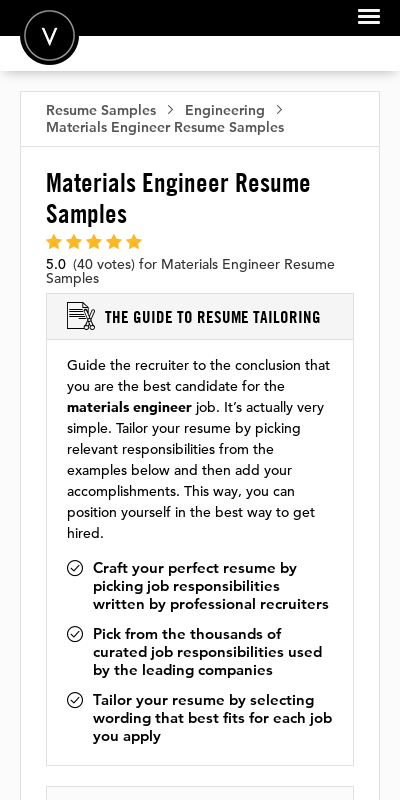
The United States is the third largest country manufacturer in the entire world. Its manufacturing output was almost double that of the Great Recession. However, despite a strong domestic economy, the United States manufacturing industry is taking a shotgun approach to its current challenges. Whether this is the result of a lack of investment or a lack of skilled labor, we need to be more aggressive about tackling the challenges facing our industry.
Jobs have declined by 5 million since 2000
The US has lost five million manufacturing jobs since 2000. While some people believe trade with China is the reason, it only accounts for a fourth to four percent of the decline in manufacturing job opportunities. In addition to trade with China, manufacturing jobs were lost in local markets that didn't compete with Chinese imports. But the reasons for the decline in manufacturing jobs are many. These are just a few of the many reasons.
During the last two decades, the US manufacturing sector lost nearly a third of its jobs. It was at 17 million in 1965 and dropped to a mere 12 million in 2010. The decline in manufacturing jobs is not due to trade. It has been caused by structural problems, such as a decrease in capital investment, output and productivity. This is not sustainable. Although productivity gains played a significant role in the decline of manufacturing jobs, they were not enough to compensate. The problem is not productivity gains but automation.
Strong demand for manufactured goods
The demand for manufactured goods in the United States remains strong, despite the fact the percentage of consumers spending on them has declined over the last few decades. In 1945, personal consumption of durable goods accounted to 58%, compared today to 28%. This is because both the manufacturing cost and the sale price have declined, but the content has increased. Therefore, computers, televisions, as well as sound equipment, have experienced a dramatic drop in cost.
The US's recovery in manufacturing activity has resulted in an increase in the production of manufactured goods. The Fifth District Manufacturing Activity Survey reveals that the demand for manufactured products is strong, with production increasing rapidly. However, supply chain problems are slowing down output. The increased production has stressed supply chains. Respondents report that they have experienced supply chain disruptions that impact their ability keep adequate inventories. The backlog of orders has increased, as well as the lead time for vendors.
The trade deficit in manufactured products has more than doubled over the past decade
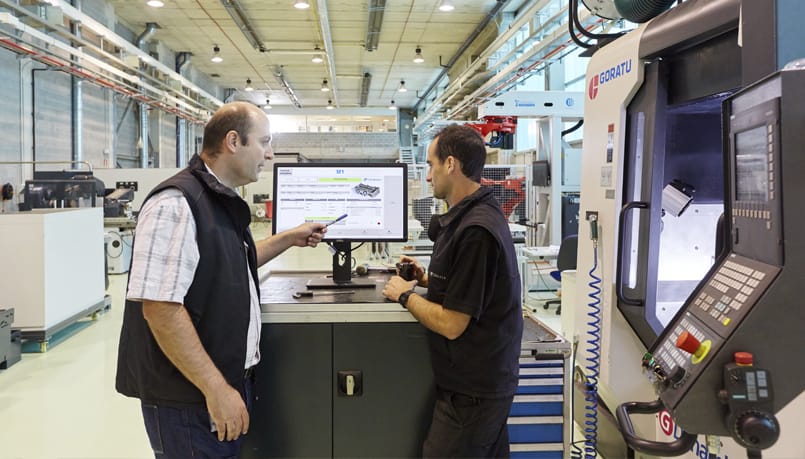
Some economists fear that the U.S.’s trade surplus will lead to lower global GDP and increase instability among its trading partners. Other economists point out that US imports are not always a good thing for the economy. They are essential to maintaining global stability. The trade deficit may even be a necessary evil, since the U.S. relies heavily on foreign markets to generate its economic output, while high levels of foreign demand may make it difficult to achieve full employment.
The U.S. trade deficit with China in manufactured goods has almost doubled since 2000. The increase in Chinese imports is partially responsible for the growing US deficit. The problem is even more severe: this imbalance is concentrated at the manufacturing sector, where wages are down and employment is declining since the 1990s. The result is that US manufacturing employment has dropped dramatically from 26 percent of 1970 to 8.5% in 2016. Some economists attribute the decline to China's increased competition, but most attribute the decline to automation, productivity increases, and demand shifting away from goods to services.
Industry adopts a shotgun approach
While the US manufacturing industry has a wide range of advanced manufacturing initiatives and is well-established in this field, some countries are taking a single-shot approach to bringing the internet of things into manufacturing. The US, by contrast, focuses on multiple technologies and mixes traditional mass media and Internet advertising. The result is a shotgun approach, where companies focus on many different technologies and aim for a broad customer base.
FAQ
What skills should a production planner have?
Being a production planner is not easy. You need to be organized and flexible. Communication skills are essential to ensure that you can communicate effectively with clients, colleagues, and customers.
What is the difference between Production Planning, Scheduling and Production Planning?
Production Planning (PP), is the process of deciding what production needs to take place at any given time. This is accomplished by forecasting the demand and identifying production resources.
Scheduling is the process of assigning specific dates to tasks so they can be completed within the specified timeframe.
What are the 7 Rs of logistics?
The acronym 7Rs of Logistics refers to the seven core principles of logistics management. It was developed by the International Association of Business Logisticians (IABL) and published in 2004 as part of its "Seven Principles of Logistics Management" series.
The acronym is made up of the following letters:
-
Responsible – ensure that all actions are legal and don't cause harm to anyone else.
-
Reliable – have faith in your ability and capability to keep promises.
-
It is reasonable to use resources efficiently and not waste them.
-
Realistic - Consider all aspects of operations, including environmental impact and cost effectiveness.
-
Respectful - show respect and treat others fairly and fairly
-
Be resourceful: Look for opportunities to save money or increase productivity.
-
Recognizable provides value-added products and services to customers
Is automation important for manufacturing?
Not only is automation important for manufacturers, but it's also vital for service providers. It allows them provide faster and more efficient services. It helps them to lower costs by reducing human errors, and improving productivity.
Is it necessary to be familiar with Manufacturing Processes before we learn about Logistics.
No. You don't have to know about manufacturing processes before learning about logistics. But, being familiar with manufacturing processes will give you a better understanding about how logistics works.
How does a production planner differ from a project manager?
A production planner is more involved in the planning phase of the project than a project manger.
Statistics
- Job #1 is delivering the ordered product according to specifications: color, size, brand, and quantity. (netsuite.com)
- According to the United Nations Industrial Development Organization (UNIDO), China is the top manufacturer worldwide by 2019 output, producing 28.7% of the total global manufacturing output, followed by the United States, Japan, Germany, and India.[52][53] (en.wikipedia.org)
- In 2021, an estimated 12.1 million Americans work in the manufacturing sector.6 (investopedia.com)
- You can multiply the result by 100 to get the total percent of monthly overhead. (investopedia.com)
- According to a Statista study, U.S. businesses spent $1.63 trillion on logistics in 2019, moving goods from origin to end user through various supply chain network segments. (netsuite.com)
External Links
How To
How to use the Just In-Time Production Method
Just-intime (JIT), which is a method to minimize costs and maximize efficiency in business process, is one way. It's a way to ensure that you get the right resources at just the right time. This means that you only pay for what you actually use. Frederick Taylor was the first to coin this term. He developed it while working as a foreman during the early 1900s. Taylor observed that overtime was paid to workers if they were late in working. He decided to ensure workers have enough time to do their jobs before starting work to improve productivity.
JIT is an acronym that means you need to plan ahead so you don’t waste your money. Look at your entire project, from start to end. Make sure you have enough resources in place to deal with any unexpected problems. You will have the resources and people to solve any problems you anticipate. You won't have to pay more for unnecessary items.
There are many JIT methods.
-
Demand-driven: This is a type of JIT where you order the parts/materials needed for your project regularly. This will allow to track how much material has been used up. It will also allow you to predict how long it takes to produce more.
-
Inventory-based : You can stock the materials you need in advance. This allows you predict the amount you can expect to sell.
-
Project-driven : This is a method where you make sure that enough money is set aside to pay the project's cost. If you know the amount you require, you can buy the materials you need.
-
Resource-based JIT : This is probably the most popular type of JIT. You assign certain resources based off demand. You will, for example, assign more staff to deal with large orders. If you don't have many orders, you'll assign fewer people to handle the workload.
-
Cost-based : This is similar in concept to resource-based. But here, you aren't concerned about how many people your company has but how much each individual costs.
-
Price-based: This is very similar to cost-based, except that instead of looking at how much each individual worker costs, you look at the overall price of the company.
-
Material-based: This is very similar to cost-based but instead of looking at total costs of the company you are concerned with how many raw materials you use on an average.
-
Time-based: This is another variation of resource-based JIT. Instead of focusing on how much each employee costs, you focus on how long it takes to complete the project.
-
Quality-based JIT: This is another variation of resource based JIT. Instead of thinking about how much each employee costs or how long it takes to manufacture something, you think about how good the quality of your product is.
-
Value-based JIT: This is the latest form of JIT. This is where you don't care about how the products perform or whether they meet customers' expectations. Instead, you focus on the added value that you provide to your market.
-
Stock-based. This method is inventory-based and focuses only on the actual production at any given point. This is used to increase production and minimize inventory.
-
Just-in-time (JIT) planning: This is a combination of JIT and supply chain management. It's the process of scheduling delivery of components immediately after they are ordered. It reduces lead times and improves throughput.